Technical Data
Machine Type : Traub TNC65DGY
Control Type : Traub TX8H
Number of Axes : 8
Main Spindle Drive : A.C. Drive with 18.5kW at 1:5.2 rating
Opposite Spindle Drive : A.C. Drive with 11kW at 1:8 rating
‘C’ axis : Yes (Main & Opposed Spindles)
Number of turrets : 2
Number of turret stations : 10 per Turret
Rotating tool drive : Yes (4000 RPM output power 4kW)
Number of driven tool stations : 2 x 10
Hydraulic chucking cylinder : Yes (Hollow)
Through tool coolant : Yes (12 bar)
High Pressure Coolant : Yes (with additional coolant filtration)
Main & Opposed Spindle : A6 Taper (65mm capacity)
Maximum speed : 4000 RPM
Turning diameter x length (chuck) : Ø175mm x 450mm
Swarf conveyor : Yes (1200mm discharge height)
Central greasing system : Yes
Additional equipment included:
Hainbuch collet chuck : 2 (Main and Opposed Spindle)
Main Spindle Collets : 10 off
Opposite Spindle Collets : 10 off
Static tool holder : 12 off various designations
Rotating tool holders : 8 off various designations
Documentation : Full Set
Basic Tool kit : Yes
Bar Feed : LNS Servo III fully interfaced compact short bar loading magazine with full set of spindle liners.
Our Refurbishment Program Revealed
You can see the in depth refurbishment we carry out here at Simon CNC Services. We pride ourselves in our rebuild program giving full attention to detail, no part of the machine gets overlooked bringing a used machine tool a new lease of life and many more years of care free production.

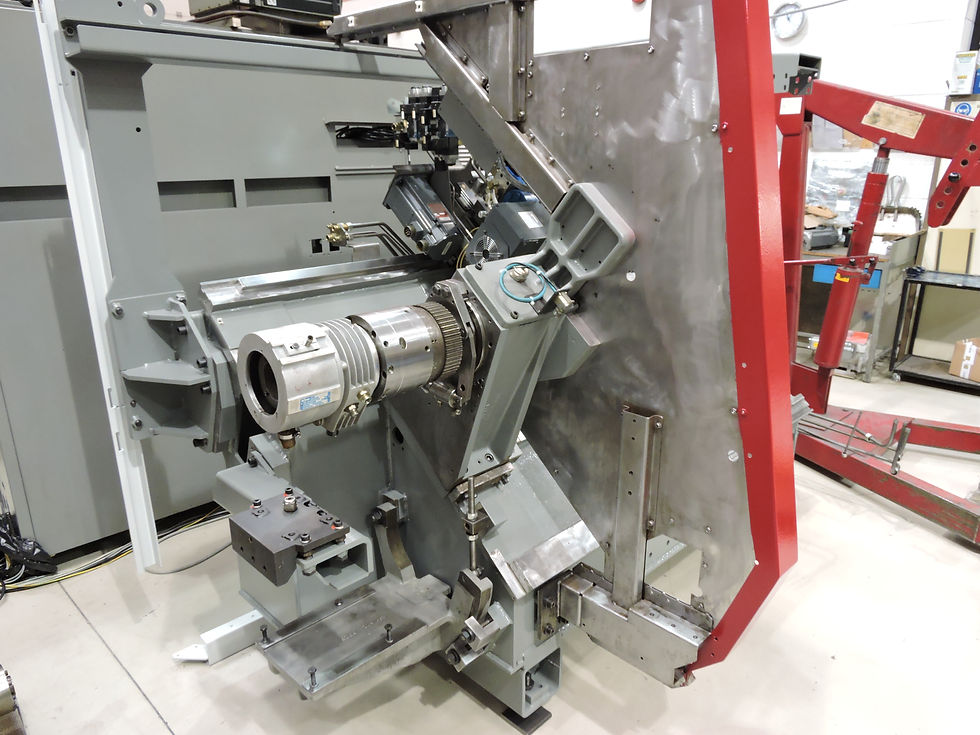


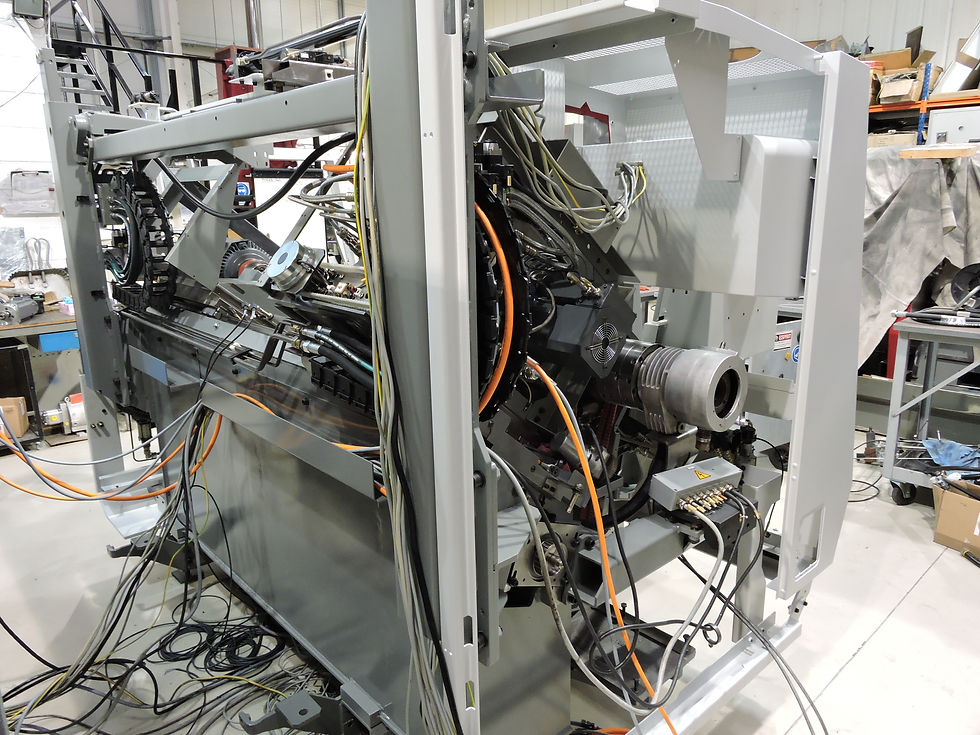
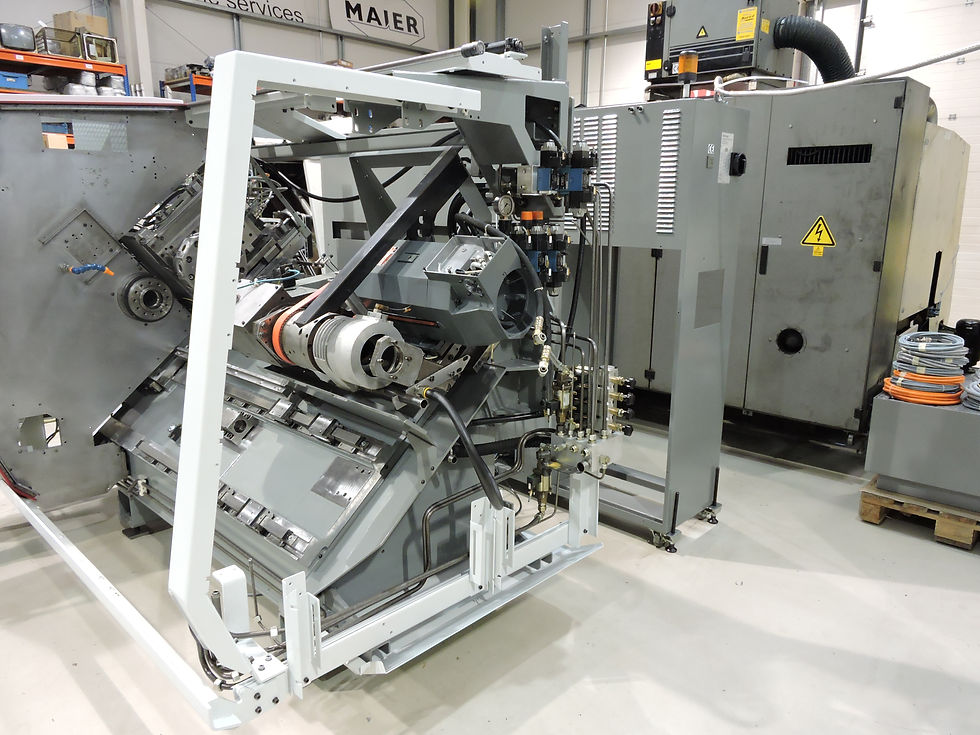

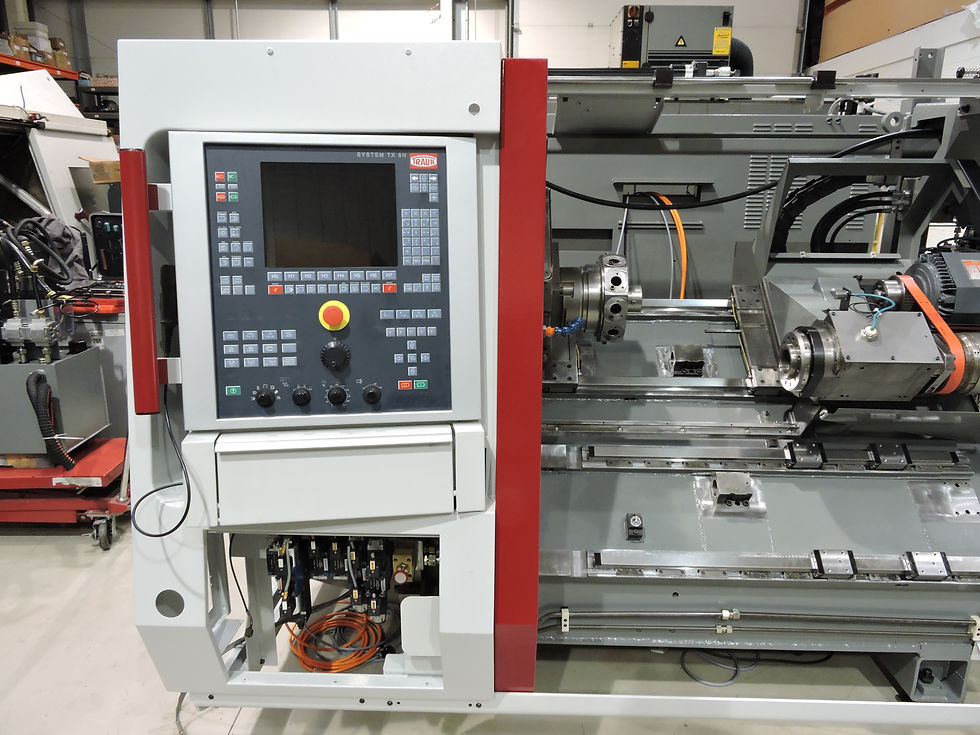


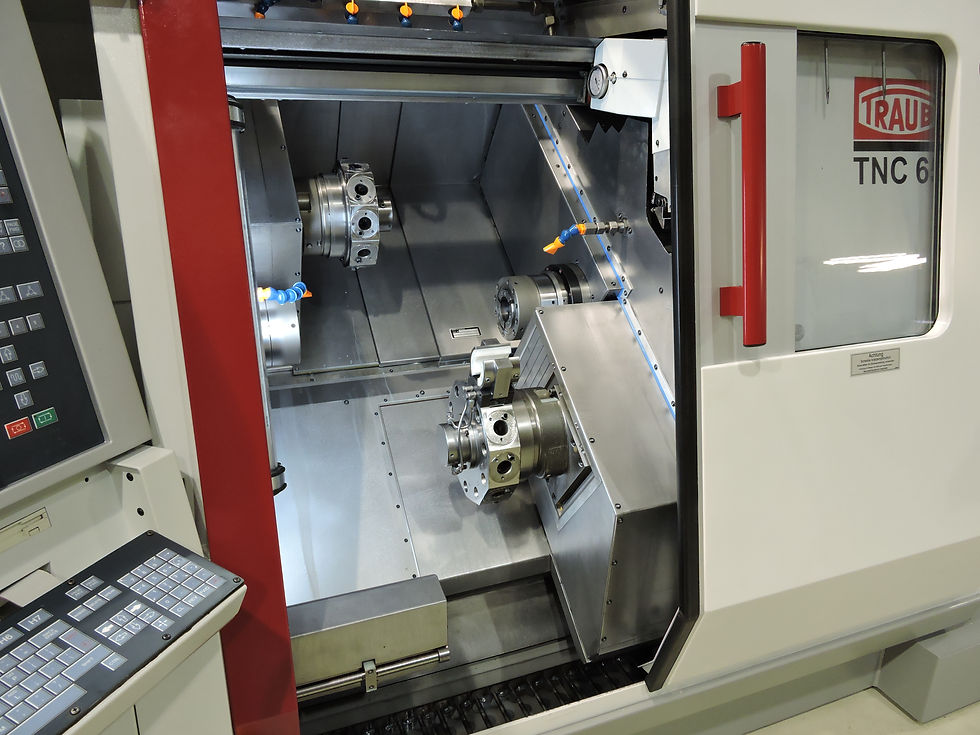


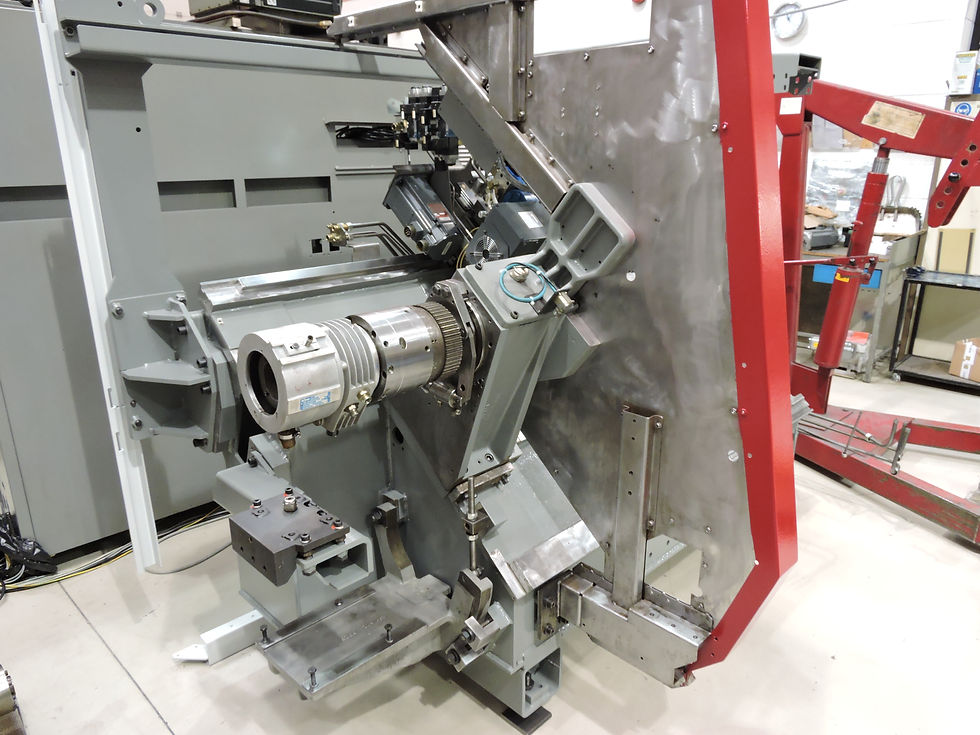


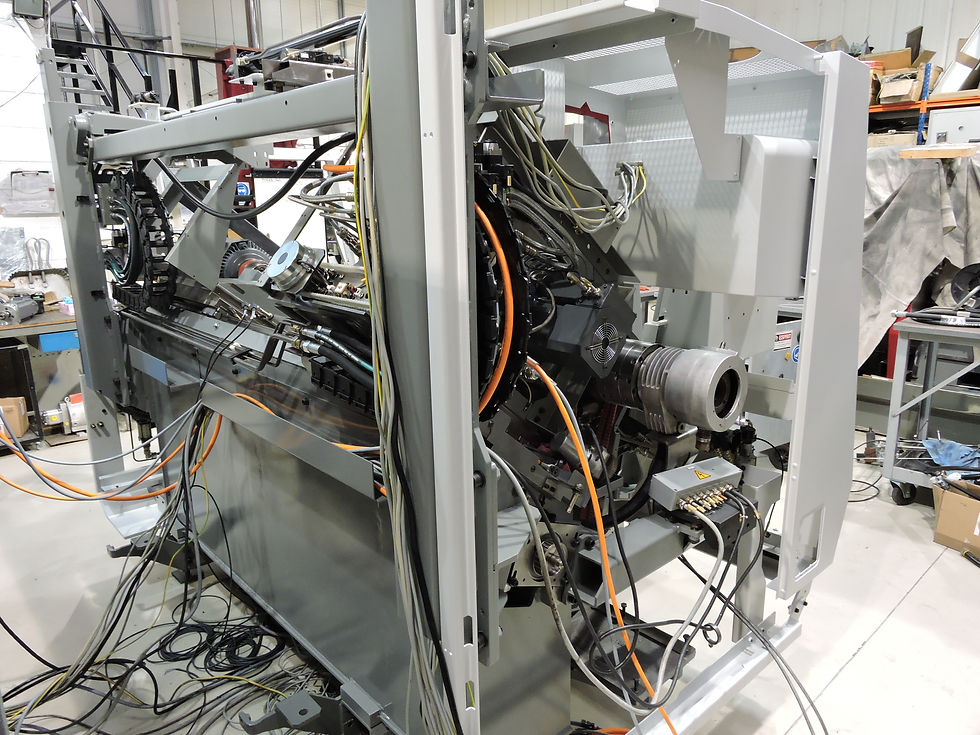
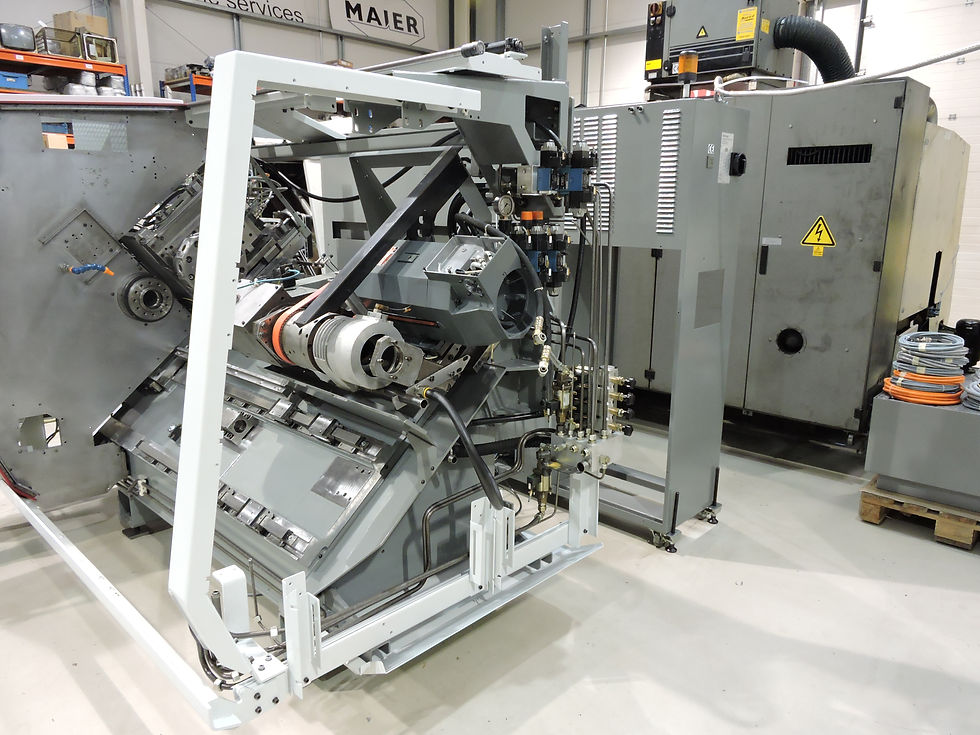

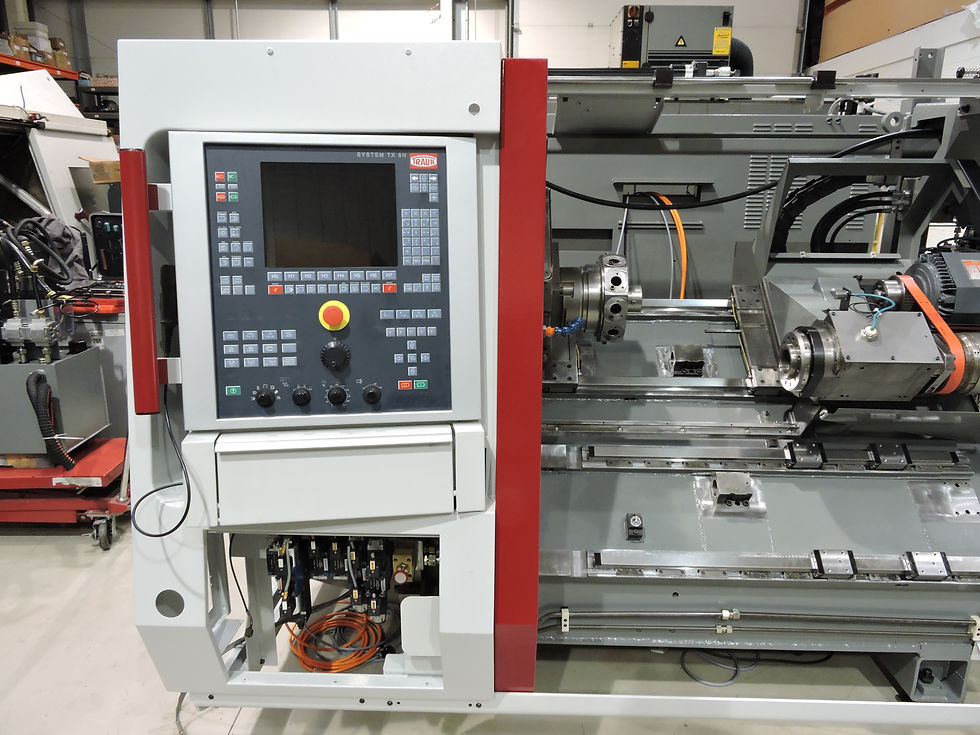


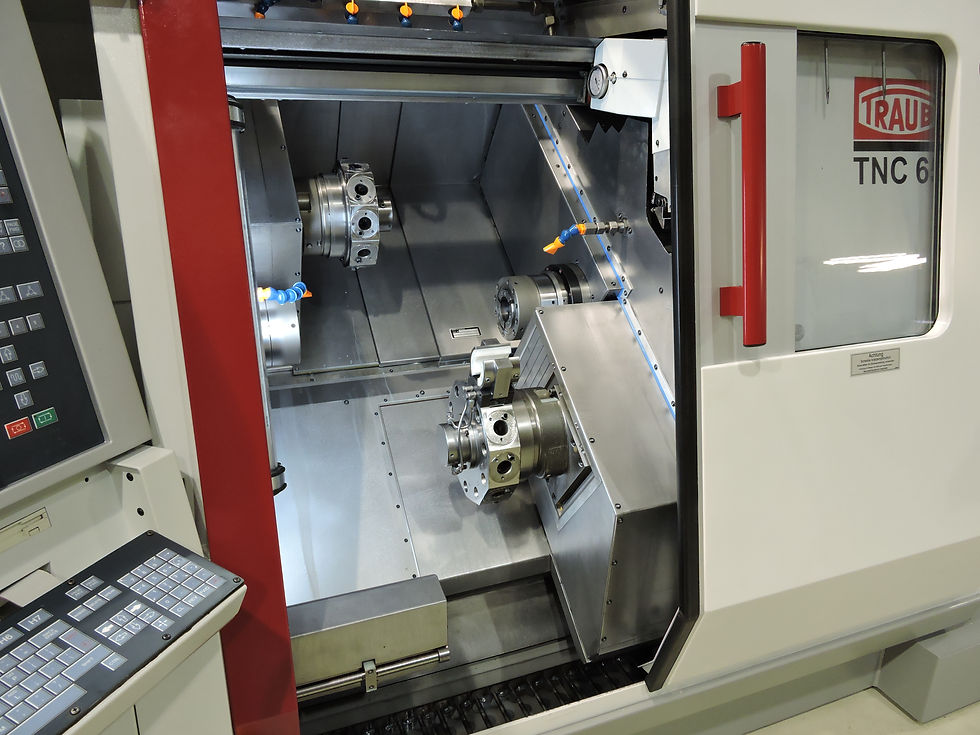

More on the TNC65
The Traub TNC65 series Mill / Turning Centre was specially designed for machining of bar stock up to 65mm diameter, With 8 NC – axes, two work spindles and two 10 station turrets (all can be driven), the machine is equipped for the most demanding production requirements.
The included ‘Y’ axis on the upper turret can handle all individual milling requirements. The tools of both turrets can be directed towards the main and opposed spindles together. Alternatively, either turret can be used to machine work pieces at either the main or opposed spindles therefore offering optimal flexibility.
For complete automation the machine is interfaced with the compact LNS Servo III short bar loading magazine. Parts removal is via a hydraulic gripper in the lower turret that transfers the finished work piece to an integral parts conveyor for transporting the work piece out of the machining area. This was added as an option as this machine was built originally with the Easy Handling System "EHS" for remnant and part removal to a shorter conveyor located at the opposed spindle side of the machine.
Further options included with this machine are a high pressure coolant filtration system, hydraulic ejector and collet flushing of the opposed spindle, high precision Hainbuch collet chucks fitted to both spindles, tool force monitoring for all tools. Included with the machine is a comprehensive package of static and driven tool holders and a selection of main and opposed spindle collets.
Get In Touch
Simon CNC Services is committed to exceeding your needs. Questions, comments or special requests? We’d love to hear from you, so don’t hesitate to reach out today.
Simon CNC Services Limited,
Unit 1, Old Brick Works Lane,
Chesterfield, S41 7JD
+44 (0)1246 224 111